Web HMI: Programming on our free and Web-based HMI Software, Viewing it on PC and Mobile Phones
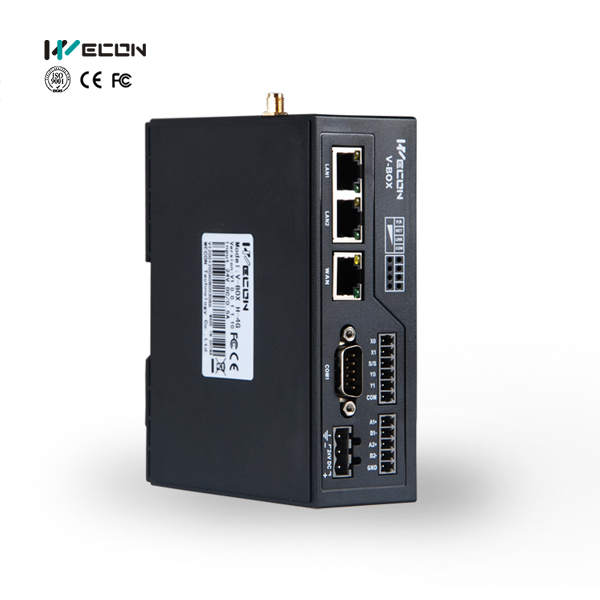
Web-based HMI with HDMI port. Cloud HMI. External Screen.
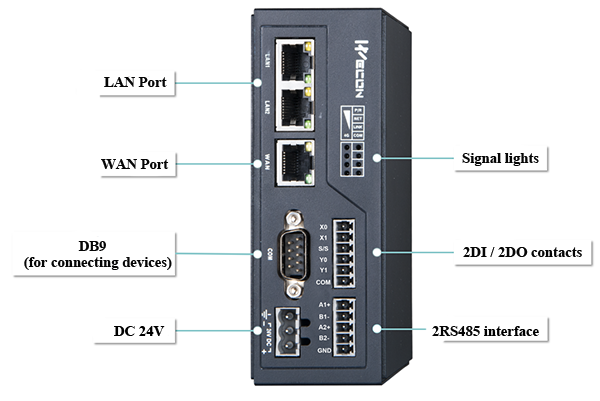
VBox-H Front Panel
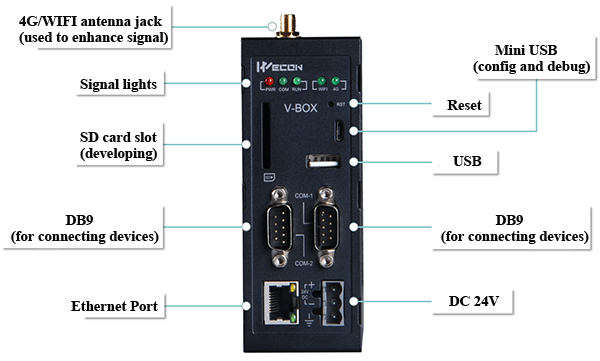
VBox-S1 Front Panel
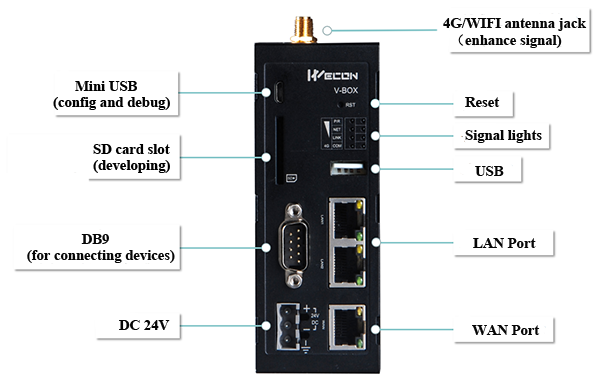
VBox-S2 Front Panel
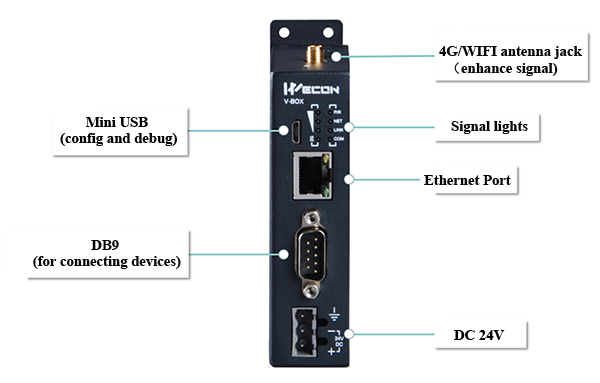
VBox-E Front Panel
Cloud Storage | E-00 | H-00 | H-WIFI | H-4G | RH |
---|---|---|---|---|---|
Live Data Points | 200 | 300 | 300 | 600 | 300 |
History Data Points | 20 | 50 | 50 | 100 | 100 |
Alarm Data Points | 50 | 200 | 200 | 300 | 200 |
Data Retention Time | 60 days or altogether 1 million | 90 days or altogether 1 million | 90 days or altogether 1 million | 180 days or altogether 1 million | 60 days or altogether 1 million |
Lua Script Support | No | Yes | Yes | Yes | Yes |
VPN Server | No | No | Yes | Yes | Yes |
Serial Port Pass-through | Yes | Yes | Yes | Yes | Yes |
Interface | 1 * USB, 1 * Ethernet Port, 1 * RS232, 1 * RS422/RS485 | 1 * USB, 2 * Ethernet Ports, 1 * RS232, 1 * RS422/RS485, 2 * RS485 | 1 * USB, 2 * Ethernet Ports, 1 * RS232, 1 * RS422/RS485, 2 * RS485, 1 * WIFI | 1 * USB, 2 * Ethernet Ports, 1 * RS232, 1 * RS422/RS485, 2 * RS485, 1 * 4G | 2 * USB, 1 * USB Type C, 2 * Ethernet Port, 2 * RS485, 1 * RS422/RS485, 1 * RS232, 1 * HDMI 1 * WIFI Optional 1 * 4G Optional |
- Main features:
- “MQTT service”, cloud storage for data, and “HTTP request” service.
- Acts as data collector and communication hub, or a bridge between data producer (PLC, VFD, Remote IO etc, Remote Sensors) and data consumer (HMI, SCADA, Mobil Phones, PC). VBox shows collected data from multiple sources and show them on Web Pages in the same way as on transitional HMI screen, other than send data to other data consumers.
- Traditional HMI screens can also connect to VBox as one other way to view and control data.
- VPN service is embedded for remotely managing HMIs and PLC devices while sitting in the comfort of your office. It’s available for upgrading and debugging HMIs and PLCs of all brands as long as doing that over Ethernet port is possible.
- Run VBox in pass-through mode to use VBox as a gateway for remotely programming and debugging PLC devices via RS232/RS485/RS422 ports. It works with not just Wecon’s own PLCs but also some models of LG, Mitsubish, Delta, Siemens, Omron, Panasonic, Xinjie PLCs. Contact us to confirm if your PLC works.
- Equipped with Web HMI and IIoT technologies, with the help of our own proprietary IIoT platform and Web HMI builder, one can easily build intuitive HMI Web Pages to show data in different ways. Scroll down to see some of these Web Pages. We currently have three IIoT servers accordingly for Chinese, European and AESEAN customers.
- To keep your data safe and private, you can use third-party IIoT platforms or your own IIoT platform to replace our IIoT platform. We’ve done the test on Google cloud, Microsoft Azure, Amazon AWS, Huawei cloud, Alibaba cloud and a few others.
- Alarm notification via SMS and Email.
- OPC-based SCADA or HMI software is supported for PC.
- LUA script is supported for advanced programming.
- All major PLC brands are supported, including MODBUS RTU and TCP as master or slave.
- 4G and WIFI available for connections.
Catalogue:
Software Tools:
- VBox Configuration App For PC
- VBox Configuration Site via HTTP
- VBox Open Cloud Site
- VBox Configuration App for iPhone – Search “V-Box” in Apple Store
- VBox Configuration App for Android (V2.0.3 09/04/2021)
- OPCTool: OPC Server connection agent (Release Date: 30/03/2021 V1.0_180714)
- VBox VPN client
Documents:
- VBOX Configuration manual via HTTP
- VBOX Configuration manual via PC
- VBOX Lua script programming manual
- VBOX VPN setup manual
- VBOX Web HMI builder manual
- VBOX Online FAQ
- VBOX Online manuals
- VBOX Online Demo Videos
Videos:
- PLC program can be remotely uploaded and updated through V-Box, find out how.
- VBOX Online Demo Videos
- VBox data configuration.
Web HMI demo pictures (contact us for address to log in and see Web HMI in action):
What is V-Box?
V-Box is a device that goes between PLC and your monitoring and controlling network. It replaces the normal role of a HMI display. Instead of showing on a HMI screen, data collected from your devices by PLCs are sent into cloud storage, which can then be accessed by smart devices, PC etc, integrated into your own software system to monitor and control your devices. This is the basic concept of IIoT. V-Box takes on the role of bringing your devices into the network of IIoT. Here to download V-Box’s introductory document and data sheet.
Where does V-Box sit in your system?
V-Box connects to PLC and other devices through Ethernet/RS485/RS422/RS232 to collect live data. Through V-Box apps (through browsers on PC or dedicated apps on smart devices), you can set up alerts and alarms, view live data, view history data etc, so that when something happens you can get first-hand notification. Using OPC clients, which have a lot of free and non-free options, you can customise your own HMI apps running on PCs to monitor and control your devices the same as you normally do on HMI displays. You can also use OPC SDK to develop your own HMI software to run on PC/Mac. Here’s a link where you can find some of the OPC sources.
What are the benefits of using V-Box?
1. V-Box is cheaper than most of HMI displays on the market.
2. All the data from your different devices can be brought together onto one computer and one app for easy management.
3. V-Box supports MODBUS TCP/RTU/ASCII and many more dedicated PLC protocols from major brands.
4. You can monitor and control your devices in the comfort of your office on a PC.
5. You can also monitor and control your devices on smart devices through dedicated apps. Alarm notifications can be sent to your mobile phones. You’ll never miss any emergencies no matter where you are.
6. By supporting OPC, you have the freedom of integrating data into your own software system to for total control.
7. If you don’t want to program from scratch, use a OPC client of your own choice to develop your own HMI app.
OPC is a software interface standard that allows Windows programs to communicate with industrial hardware devices.

OPC is implemented in server/client pairs. The OPC server is a software program that converts the hardware communication protocol used by a PLC [3] into the OPC protocol. The OPC client software is any program that needs to connect to the hardware, such as an HMI [4] . The OPC client uses the OPC server to get data from or send commands to the hardware. The value of OPC is that it is an open standard, which means lower costs for manufacturers and more options for users. Hardware manufacturers need only provide a single OPC server for their devices to communicate with any OPC client. Software vendors simply include OPC client capabilities in their products and they become instantly compatible with thousands of hardware devices. Users can choose any OPC client software they need, resting assured that it will communicate seamlessly with their OPC-enabled hardware, and vice-versa. The typical OPC connection scenario is a single server-client connection on a single computer as illustrated above, but there are more possibilities.
The Industrial Internet of Things (IIoT)
What is it and How Will it Affect Manufacturing?
The IIoT is part of a larger concept known as the Internet of Things (IoT). The IoT is a network of intelligent computers, devices, and objects that collect and share huge amounts of data. The collected data is sent to a central Cloud-based service where it is aggregated with other data and then shared with end users in a helpful way. The IoT will increase automation in homes, schools, stores, and in many industries.
The application of the IoT to the manufacturing industry is called the IIoT (or Industrial Internet or Industry 4.0). The IIoT will revolutionize manufacturing by enabling the acquisition and accessibility of far greater amounts of data, at far greater speeds, and far more efficiently than before. A number of innovative companies have started to implement the IIoT by leveraging intelligent, connected devices in their factories.
What are the Benefits of IIoT?
The IIoT can greatly improve connectivity, efficiency, scalability, time savings, and cost savings for industrial organizations. Companies are already benefitting from the IIoT through cost savings due to predictive maintenance, improved safety, and other operational efficiencies. IIoT networks of intelligent devices allow industrial organizations to break open data silos and connect all of their people, data, and processes from the factory floor to the executive offices. Business leaders can use IIoT data to get a full and accurate view of how their enterprise is doing, which will help them make better decisions.
IIoT Protocols
One of the issues encountered in the transition to the IIoT is the fact that different edge-of-network devices have historically used different protocols for sending and receiving data. While there are a number of different communication protocols currently in use, such as OPC-UA, the Message Queueing Telemetry Transport (MQTT) transfer protocol is quickly emerging as the standard for IIoT, due to its lightweight overhead, publish/subscribe model, and bidirectional capabilities. You can read more about MQTT here.
Challenges of the IIoT
Interoperability and security are probably the two biggest challenges surrounding the implementation of IIoT. As technology writer Margaret Rouse observes, “A major concern surrounding the Industrial IoT is interoperability between devices and machines that use different protocols and have different architectures.” Ignition is an excellent solution for this since it is cross-platform and built on open-source, IT-standard technologies.
Companies need to know that their data is secure. The proliferation of sensors and other smart, connected devices has resulted in a parallel explosion in security vulnerabilities. This is another factor in the rise of MQTT since it is a very secure IIoT protocol.
The Future of the IIoT
The IIoT is widely considered to be one of the primary trends affecting industrial businesses today and in the future. Industries are pushing to modernize systems and equipment to meet new regulations, to keep up with increasing market speed and volatility, and to deal with disruptive technologies. Businesses that have embraced the IIoT have seen significant improvements to safety, efficiency, and profitability, and it is expected that this trend will continue as IIoT technologies are more widely adopted.
The Ignition IIoT solution greatly improves connectivity, efficiency, scalability, time savings, and cost savings for industrial organizations. It can unite the people and systems on the plant floor with those at the enterprise level. It can also allow enterprises to get the most value from their system without being constrained by technological and economic limitations. For these reasons and more, Ignition offers the ideal platform for bringing the power of the IIoT into your enterprise.